What is Destructive Testing?
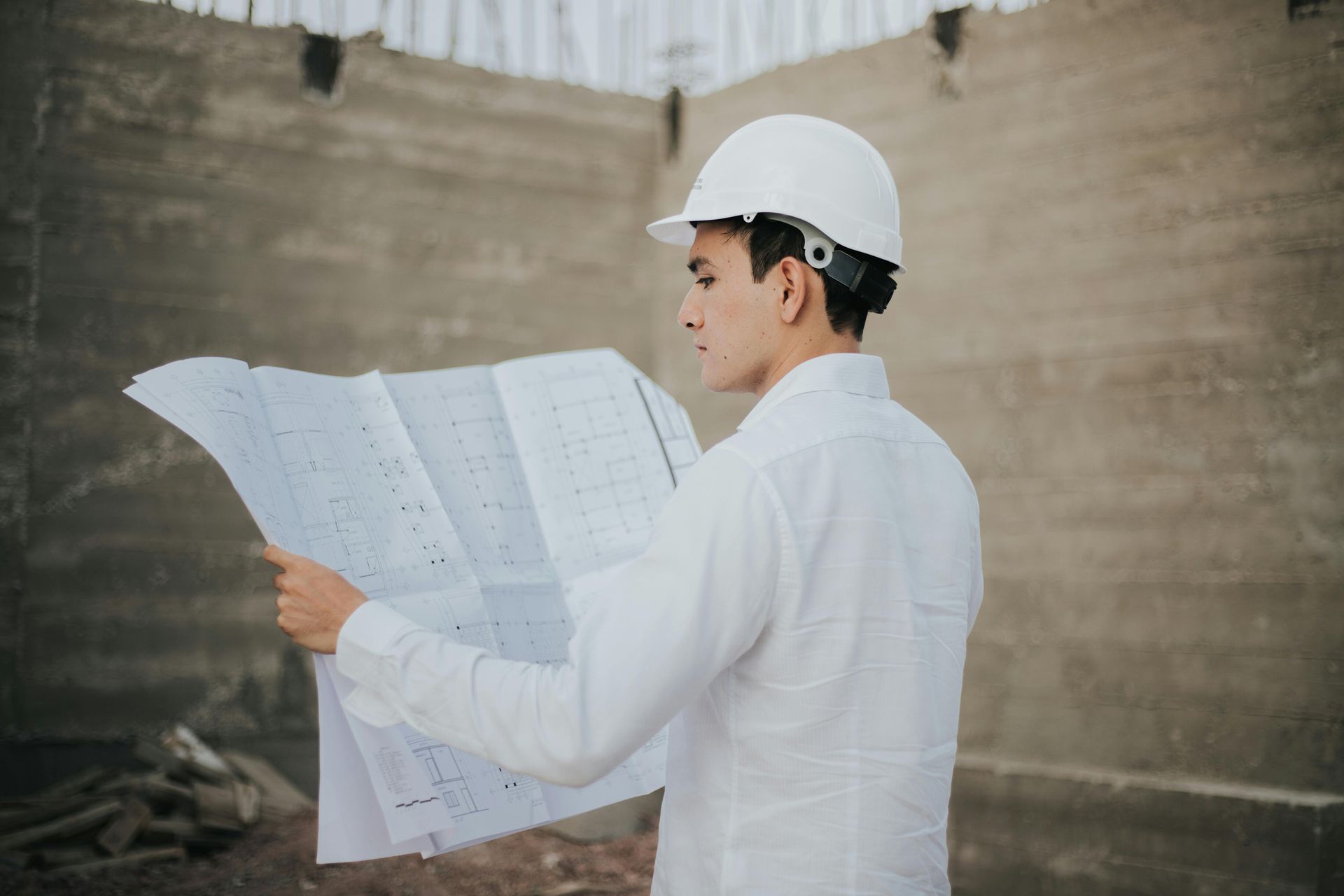
Destructive testing is a process used to evaluate the structural integrity of a building by intentionally removing, dismantling, or applying stress to materials. This method is commonly used in construction defect investigations, structural assessments, and quality assurance to uncover hidden defects that could lead to costly repairs or safety hazards.
How Destructive Testing Works
Destructive testing involves controlled damage to a structure or material to determine its durability, resistance, and failure points. Unlike non-destructive testing (NDT), which evaluates a structure without causing damage, destructive testing (DT) ensures a deeper investigation of potential issues.
Common Types of Destructive Testing
- Water Testing – Identifies leaks and water intrusion in windows, walls, and other openings.
- Roof Testing – Assesses the durability of roofing materials and detects potential weaknesses.
- Wall and Floor Openings – Helps uncover structural deficiencies hidden within walls, floors, and ceilings.
- Material Testing – Evaluate the strength and resilience of construction materials such as concrete, wood, and steel.
- Structural Dismantling – Removes sections of a structure to expose potential internal defects.
These tests provide critical insights into a building’s weaknesses, helping contractors and property owners plan necessary repairs and reinforcements.
Why Destructive Testing is Important in Construction
Destructive testing is crucial in identifying hidden structural issues, preserving property value, and ensuring long-term safety. Many defects are not visible during routine inspections, making intrusive testing essential for accurate assessments and informed decision-making.
Early Problem Detection
Many structural issues remain hidden behind walls, floors, or roofing materials. Destructive testing helps detect:
- Water intrusion that causes mold, rot, and long-term material degradation.
- Weak structural elements that may lead to safety hazards.
- Improper material use or poor construction techniques that could fail under stress.
Increased Property Value
A well-maintained property holds its value better than one with hidden defects. Homeowners and HOAs benefit from destructive testing because:
- Structural assessments ensure long-term stability and safety.
- Repairs and reinforcements make properties more attractive to buyers.
- Detecting and fixing minor defects early prevents expensive renovations later.
Long-Term Cost Savings
While destructive testing requires an upfront investment, it prevents significant financial burdens in the future. Fixing minor problems today can save homeowners and property managers from:
- Full-scale structural replacements are caused by untreated deterioration.
- Extensive mold remediation due to unnoticed leaks.
- Emergency repairs could have been avoided with early intervention.
Enhanced Safety
Undetected structural issues can pose serious risks to occupants. Destructive testing helps uncover potential dangers, such as:
- Wood rot weakened supports, and unstable structures could lead to collapses.
- Electrical hazards, exposed wiring, and gas leaks that increase the risk of fires.
- Deteriorating materials and hidden corrosion that compromise structural integrity.
Regulatory Compliance
Many local building codes and insurance policies require periodic structural testing to ensure legal compliance. Destructive testing helps:
- Meet regulatory standards for construction, remodeling, and property maintenance.
- Ensure compliance with HOA and insurance requirements, reducing the risk of denied claims or penalties.
- Verify material durability and safety before major renovations or structural modifications.
Staying compliant with building regulations protects property owners from legal and financial consequences.
Informed Decision-Making
HOAs and property managers need precise, data-backed assessments to make informed maintenance and budgeting decisions. Destructive testing provides:
- Accurate reports detailing structural weaknesses and areas needing repairs.
- A roadmap for future maintenance, ensuring repairs are prioritized effectively.
- Cost-effective solutions by identifying which defects require immediate attention versus long-term monitoring.
Destructive vs. Non-Destructive Testing
Both destructive testing (DT) and non-destructive testing (NDT) play essential roles in construction.
- Destructive testing is used when surface-level inspections are not enough. It provides a deep analysis of material strength, water penetration, and structural stability.
- Non-destructive testing methods, such as thermal imaging, ultrasound, and moisture meters, detect surface-level issues and are ideal for routine maintenance.
While NDT is non-invasive, it may not detect hidden internal issues. DT is necessary when there is a need for thorough defect identification and accurate repair planning. For more details on non-destructive testing, visit The American Society for Nondestructive Testing (ASNT).
Safety Considerations for Destructive Testing
Since destructive testing involves cutting, dismantling, and exposing materials, safety precautions are essential.
Key Safety Measures
- Personal Protective Equipment (PPE) – Workers should wear gloves, safety goggles, helmets, and dust masks.
- Controlled Testing Areas – Ensuring the testing site is secure prevents accidents or additional property damage.
- Proper Equipment Handling – Using tools like saws, drills, and testing machines safely reduces risks.
- Regulatory Compliance – All testing should follow building codes and safety guidelines to ensure proper execution.
For official safety standards, refer to OSHA’s Construction Safety Standards. These guidelines outline the required protective measures, training, and protocols that workers and contractors must follow when performing destructive testing, structural dismantling, and material assessments.
Professional Services
For homeowners, HOAs, and property managers, working with experienced professionals for destructive testing is essential. EmpireWorks specializes in intrusive testing and reconstruction, ensuring a detailed and reliable assessment of structural issues.
What EmpireWorks Offers:
- Water testing to identify leaks and moisture issues.
- Roof testing to assess material durability.
- Wall and floor opening inspections to uncover hidden defects.
- Material testing to evaluate the strength and resilience of construction materials.
- Structural dismantling to expose underlying issues for accurate defect analysis.
EmpireWorks provides white-glove service, ensuring that testing is conducted efficiently, safely, and with minimal disruption. Whether it’s an HOA-wide inspection or a single-property assessment, their team delivers professional and accurate results.
Conclusion
Destructive testing is essential for property safety, maintenance, and value preservation, uncovering hidden defects, preventing costly repairs, and ensuring materials meet high standards. EmpireWorks provides expert assessments to keep properties in top condition. Contact them today for professional testing and repair solutions.
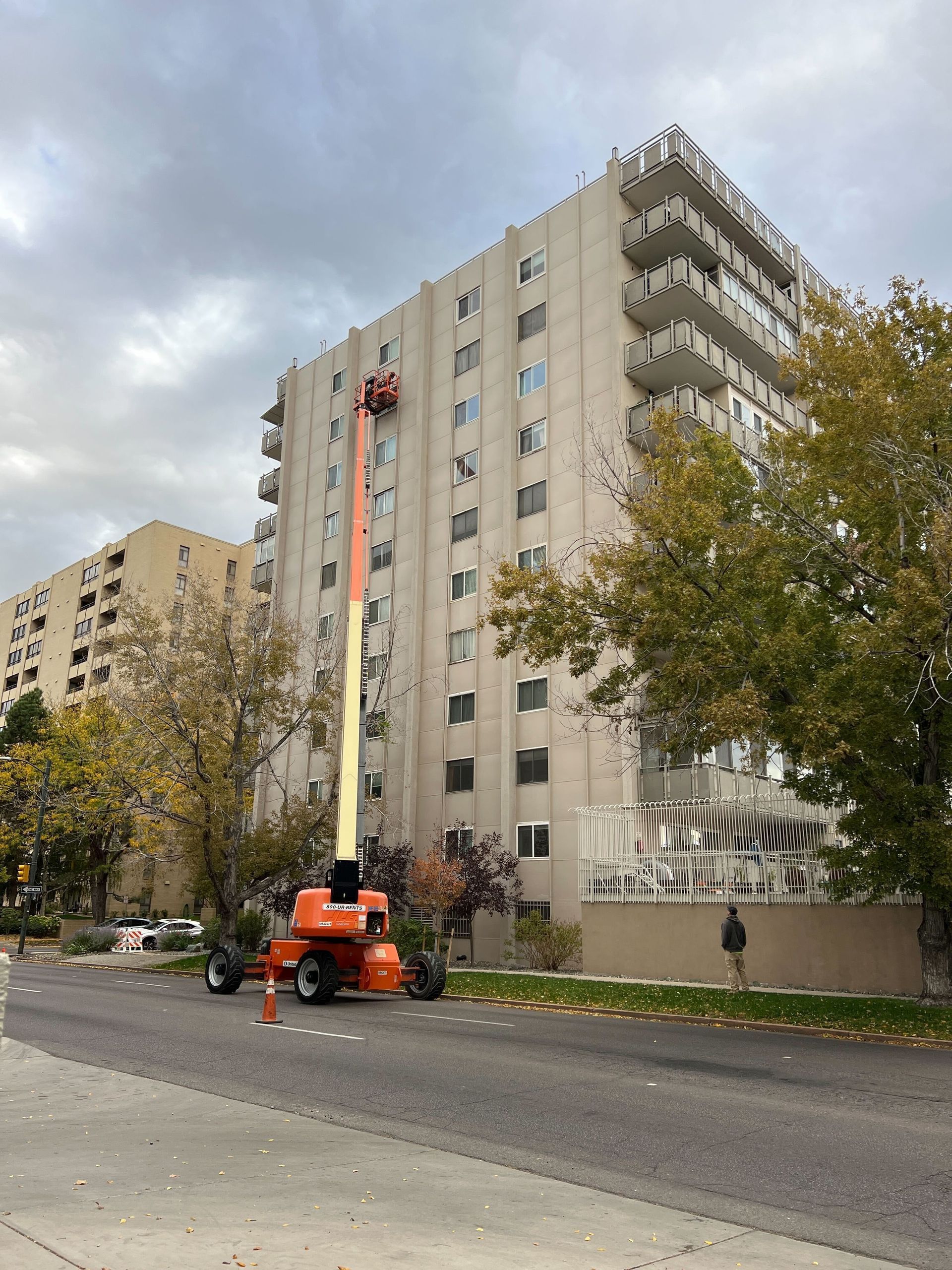
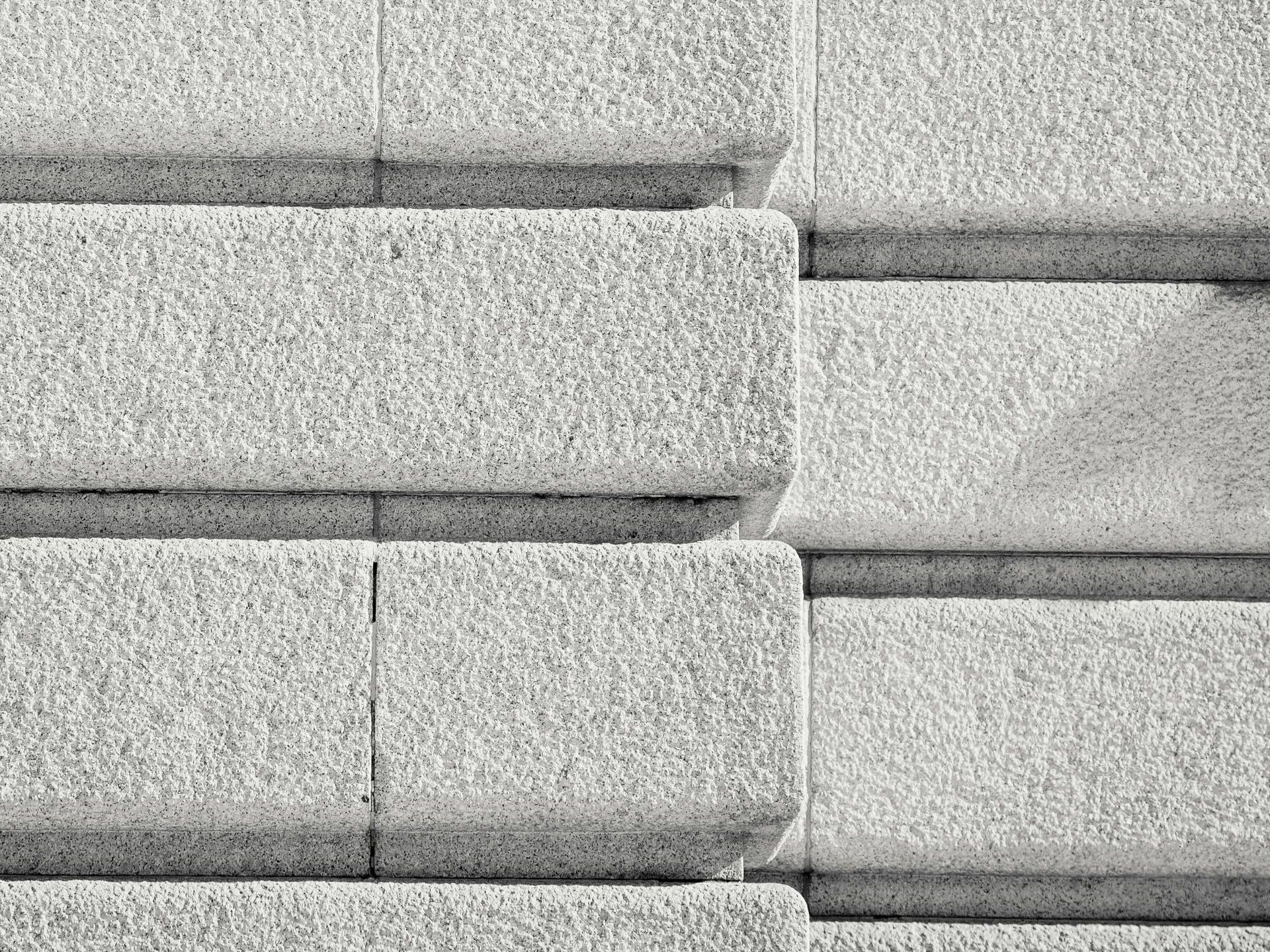
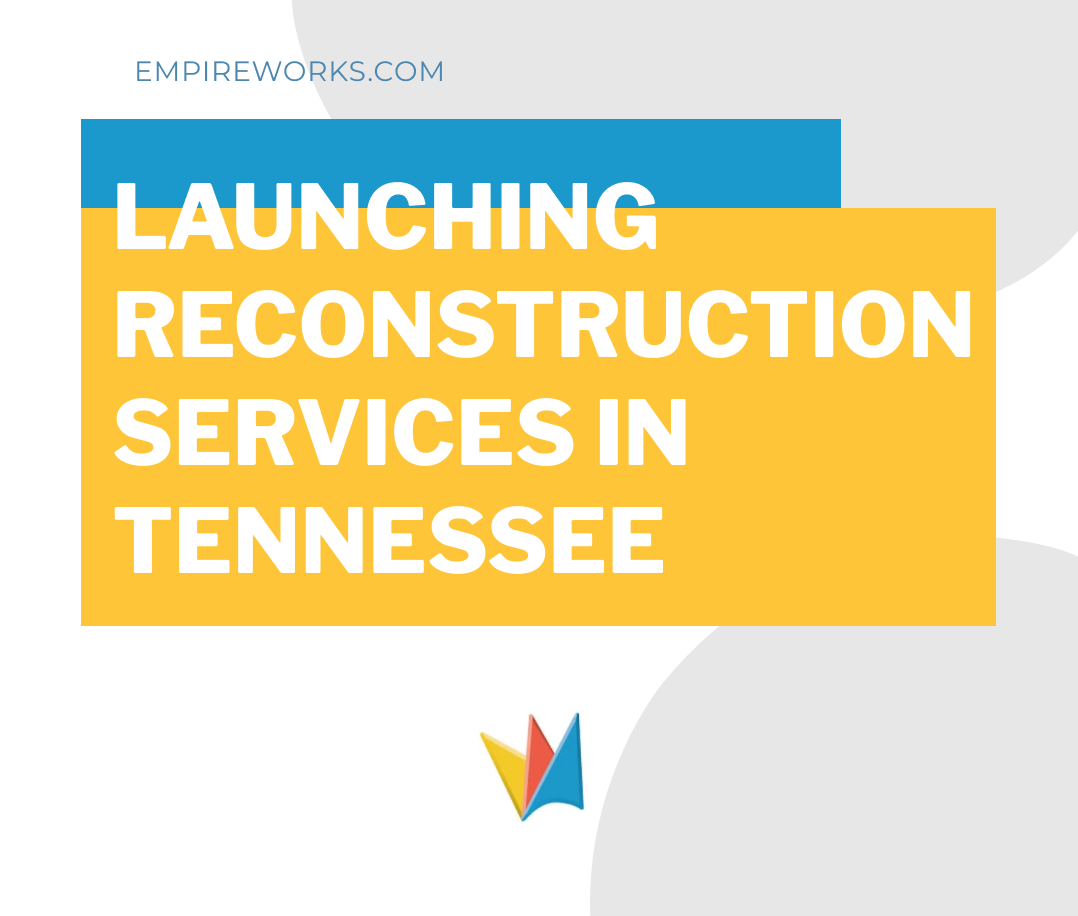
EmpireWorks Reconstruction Launches Top-Tier Reconstruction Services to Middle Tennessee Communities
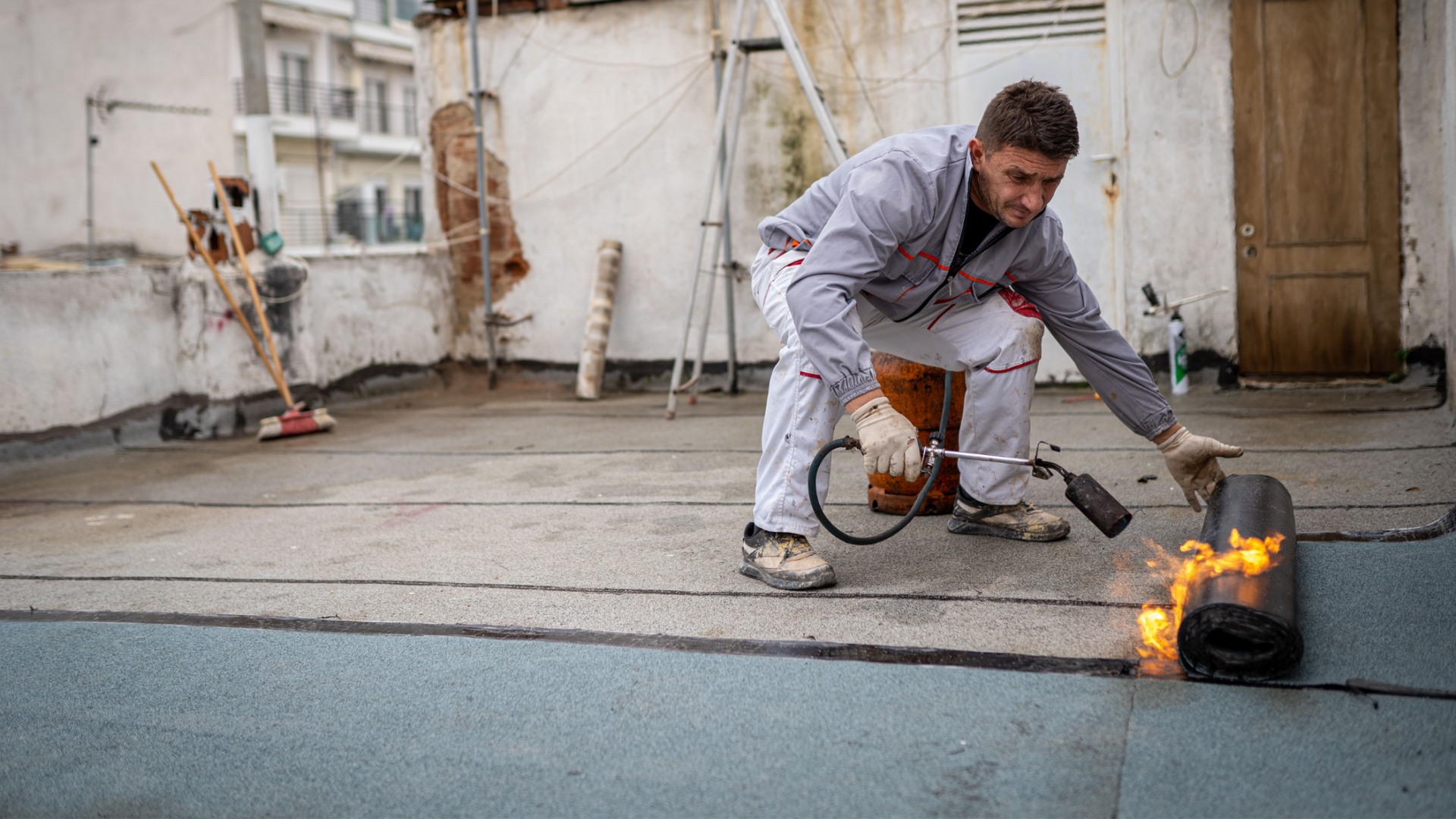
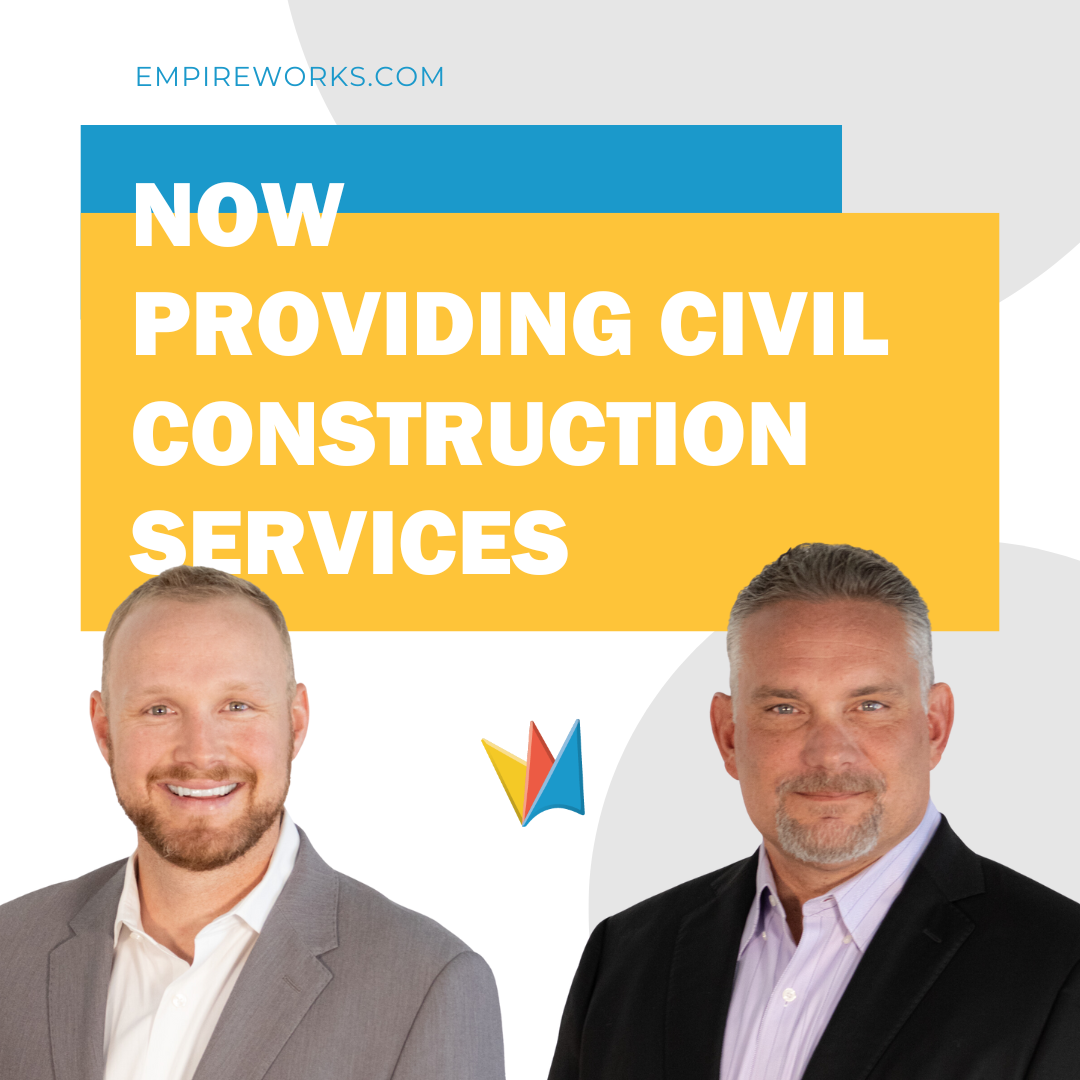