How Often Should EIFS Be Inspected?
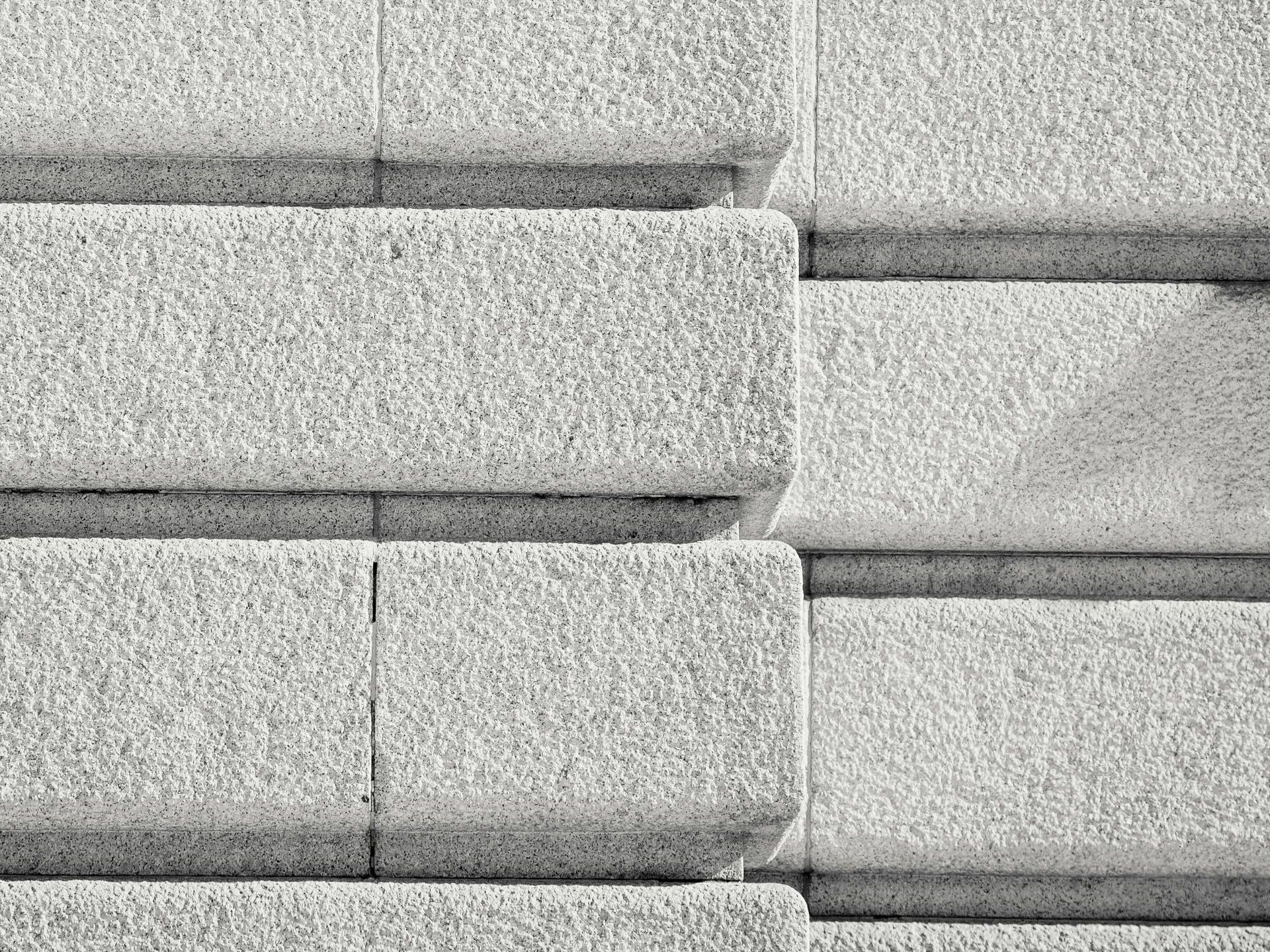
Exterior Insulation and Finish Systems (EIFS) are a popular choice for cladding thanks to their energy efficiency, durability, and aesthetic versatility. Like any exterior component of a building, EIFS requires regular care and inspections to maintain its performance and appearance. This guide explores how often EIFS should be inspected, what to look for, and how inspections can help you protect your investment.
Understanding EIFS and Its Importance
EIFS is a lightweight cladding system that provides insulation and a decorative finish. It consists of multiple layers, including insulation boards, a base coat with reinforcing mesh, and a durable finish coat. While it’s often referred to as synthetic stucco, EIFS is a unique system that offers several advantages for residential and commercial buildings.
What Is EIFS?
EIFS was developed in the 1950s and has since become a go-to solution for energy-efficient cladding. The system acts as a thermal blanket for buildings, reducing heat loss and lowering energy costs. Its lightweight design reduces structural strain while allowing for creative architectural details like arches, columns, and custom textures.
Benefits of EIFS for Buildings
EIFS offers a variety of benefits that make it a standout choice for building owners:
- Energy Efficiency: Reduces heat transfer, leading to smaller HVAC systems and lower utility bills.
- Durability: Withstands harsh weather, resists cracking, and retains its appearance for years.
- Aesthetic Flexibility: Comes in a range of colors, textures, and finishes to match any design vision.
- Low Maintenance: Requires minimal upkeep compared to other cladding systems.
How Often Should EIFS Be Inspected?
Regular EIFS inspections are crucial for maintaining its performance and preventing costly repairs. Depending on the type of system, environmental factors, and any visible signs of damage, inspection schedules may vary. Let’s break down when and why inspections should occur.
Annually for Barrier Systems
Barrier EIFS relies on a sealed exterior to prevent water intrusion. Without a drainage system, even minor sealant failures or cracks can allow moisture to penetrate behind the cladding. Since all sealants degrade over time and weather conditions can accelerate this process, annual inspections are highly recommended for barrier systems.
Annual checks are especially important in regions with high humidity or frequent rain, as these conditions increase the risk of moisture-related damage. During these inspections, professionals check for:
- Deteriorating sealants around windows, doors, and joints.
- Cracks or punctures in the finish coat that could allow water entry.
- Moisture buildup or soft spots in the substrate.
Every Two to Three Years for Water-Managed Systems
Water-managed EIFS includes a drainage layer that helps redirect incidental moisture away from the building. This design provides extra protection against water damage, allowing for less frequent inspections—typically every two to three years.
Inspections focus on:
- Ensuring that drainage components, such as weep holes or flashing, are functioning properly.
- Verifying that the exterior finish and sealants remain intact to prevent excessive moisture exposure.
- Checking for debris or blockages in drainage channels that could hinder water flow.
After Major Weather Events
Extreme weather conditions, such as hailstorms, heavy rains, strong winds, or snowstorms, can cause sudden damage to EIFS. Inspecting the system immediately after such events is critical to identify and repair potential issues before they worsen. Key weather-related problems include:
- Hail or debris impact causing cracks or holes in the finish coat.
- Water infiltration due to wind-driven rain or damaged flashing.
- Structural shifts that lead to gaps or stress cracks in the system.
Even if damage is not immediately visible, underlying issues like moisture intrusion can develop. Professional post-storm inspections help catch these hidden problems early.
Whenever You Notice Issues
Signs of damage or wear should never be ignored. Cracks, stains, or peeling finishes may seem minor but could indicate more serious underlying problems, such as water infiltration or structural compromise. Prompt inspections are necessary to assess the extent of the damage and determine the best course of action.
Visible warning signs include:
- Dark stains or discoloration are often a sign of trapped moisture.
- Cracks or gaps around windows, doors, or other penetrations.
- Bubbling, sagging, or bulging areas on the EIFS surface.
- Mold growth or a musty smell indoors suggests hidden moisture issues.
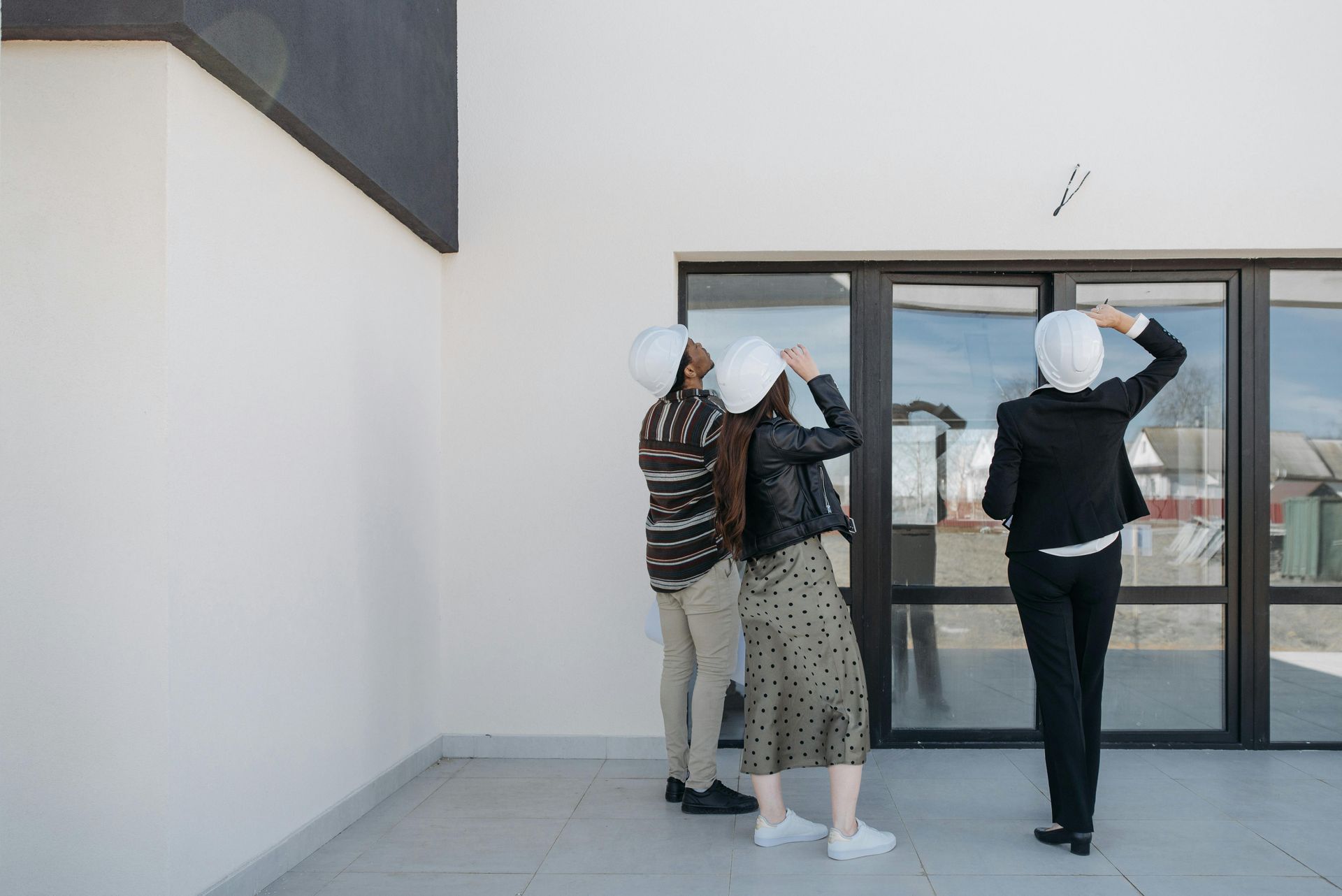
Why Regular EIFS Inspections Are Necessary
EIFS inspections are a vital component of building maintenance. While EIFS offers durability and low maintenance compared to other cladding systems, it is not immune to wear and potential damage. Regular inspections help identify problems early, keeping the system functional and aesthetically pleasing while preventing costly repairs.
Common Issues Detected During Inspections
EIFS problems often start small but can escalate quickly if not addressed. Inspections are designed to catch these issues before they lead to significant damage:
Moisture Intrusion
Water is the number one enemy of any cladding system, and EIFS is no exception. Moisture can seep into the system through cracks, gaps, or deteriorated sealants, leading to:
- Mold and mildew growth can affect indoor air quality.
- Rotting of wooden substrates, weakening the building’s structure.
- Corrosion in metal framing or other internal components.
Inspections focus on spotting areas where water intrusion is most likely, such as around windows, doors, and roofline intersections.
Cracking or Deterioration
Over time, EIFS can develop cracks in its finish coat or base layer. These cracks may seem cosmetic but can compromise the system’s integrity, allowing moisture to penetrate. Common causes of cracking include:
- Thermal expansion and contraction of building materials.
- Impact from hail or debris.
- Poor installation practices.
Inspectors assess the size and location of cracks to determine whether repairs are necessary to restore the cladding’s protective barrier.
Sealant Failures
Sealants are essential for maintaining a watertight EIFS system. Over time, exposure to UV rays, temperature changes, and moisture can degrade sealants, leading to gaps or detachment. This creates entry points for water and air, which can compromise both the system’s insulation and its structural integrity. Inspections often involve checking the condition of sealants around penetrations, joints, and edges.
Role of Inspections in Longevity and Performance
Routine inspections are more than just preventive measures; they are investments in the long-term health of your EIFS system. Here’s how inspections contribute to its longevity and performance:
- Extending System Lifespan: Regular checks ensure that minor issues, like hairline cracks or deteriorated sealants, are fixed promptly. This prevents minor problems from snowballing into major repairs or requiring complete system replacement.
- Maintaining Aesthetic Appeal: Inspections help preserve the visual integrity of EIFS by identifying areas of discoloration, staining, or peeling. Addressing these issues early keeps your building looking clean and professional.
- Reducing Repair Costs: Early detection is key to cost savings. Repairing a small crack or replacing a section of deteriorated sealant is significantly less expensive than addressing widespread water damage or structural rot.
- Enhancing Energy Efficiency: Moisture infiltration or air leaks caused by damaged EIFS can reduce the system’s insulating properties, leading to higher energy costs. Inspections help identify these inefficiencies and restore the system’s thermal performance.
Recommended Inspection Frequency for Different Scenarios
The frequency of EIFS inspections isn’t one-size-fits-all. Factors like the type of system, environmental conditions, and the building’s age play a significant role in determining how often inspections should be conducted. By tailoring your inspection schedule to your building’s specific needs, you can ensure that your EIFS system remains in top condition for years to come.
General Guidelines for Routine Inspections
For most buildings, EIFS should be inspected every one to three years under normal conditions. Barrier systems, which rely entirely on a sealed exterior to prevent moisture intrusion, should be inspected annually. Water-managed systems, designed with drainage capabilities to handle incidental moisture, typically require inspections every two to three years.
Routine inspections help identify issues early, ensuring minor problems don’t escalate into major repairs. For property managers or owners overseeing multiple buildings, scheduling inspections on a rotational basis can be an efficient way to stay ahead of potential issues.
Factors That Influence Inspection Frequency
Certain conditions make some buildings more susceptible to wear and damage, necessitating more frequent inspections.
Climate
Buildings located in areas with extreme or unpredictable weather conditions require closer monitoring.
- Heavy Rain: Persistent rain increases the risk of water infiltration, particularly if flashing or sealants are compromised.
- Hailstorms: Hail can cause cracks or dents in the finish coat, which may allow moisture to seep into the system.
- Freezing Temperatures: Freeze-thaw cycles can cause sealants to expand and contract, leading to gaps or cracks over time.
In these regions, inspections should occur annually or even semi-annually, especially after significant weather events.
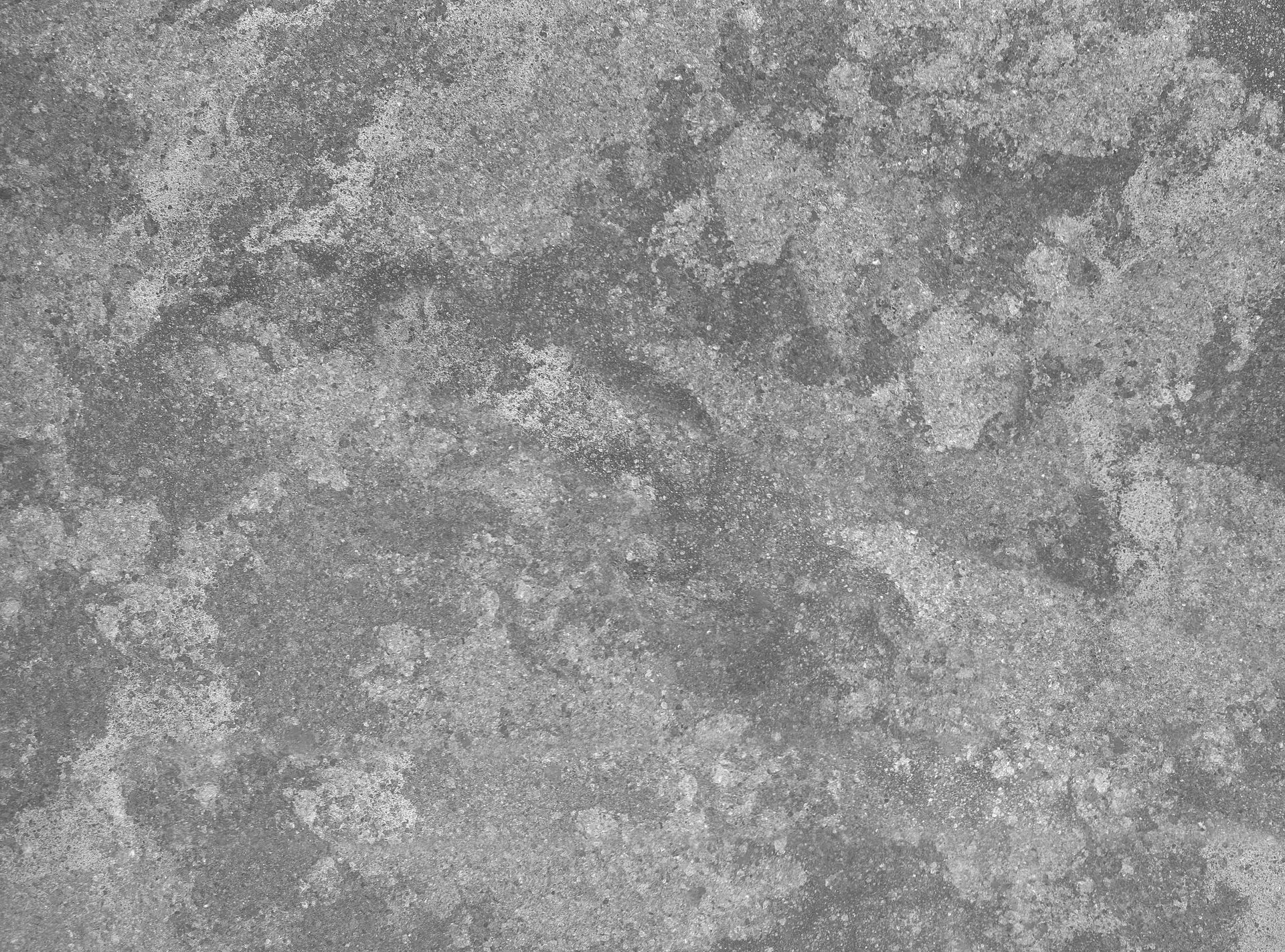
Age
The older the EIFS system, the more likely it is to have experienced wear and tear.
- Older EIFS installations, particularly those predating the adoption of water-managed systems in the late 1990s, often rely on barrier technology, which is more prone to moisture-related issues.
- Over time, sealants degrade, and small cracks can form due to natural structural shifts or weather exposure.
- Aging systems may also have outdated installation techniques that do not meet modern standards, making regular inspections critical.
For systems more than 15–20 years old, annual inspections are advisable, regardless of climate or type, to address any developing vulnerabilities.
Exposure
The building’s location and orientation can significantly affect the wear rate of its EIFS.
- High Sun Exposure: Prolonged UV exposure can cause discoloration, fading, or deterioration of the finish coat, especially on south- and west-facing walls.
- Water Proximity: Buildings located near bodies of water, such as lakes or oceans, often experience higher humidity levels, increasing the risk of mold and moisture damage.
- Urban or Industrial Environments: Pollution and airborne particles can accumulate on the EIFS surface, requiring frequent cleaning and inspection to maintain its appearance and integrity.
What to Look for During an EIFS Inspection
A thorough EIFS inspection covers both the visible exterior and hidden components of the system.
Visual Signs of Damage
Some issues can be identified with a visual inspection:
- Cracks, holes, or missing pieces in the finish coat.
- Stains or discoloration could indicate moisture intrusion.
- Sagging areas or bubbles on the surface suggest trapped water.
- Gaps or loose sealants around windows, doors, and other openings.
Tools and Techniques Used by Inspectors
Professional inspectors use advanced tools to assess the system's condition:
- Moisture Meters: Detect moisture levels within the system.
- Probes: Pin-type meters that measure moisture and assess substrate condition.
- Infrared Scanning: Identifies temperature variations that indicate water penetration.
Seek Professional Help
Maintaining and inspecting EIFS systems requires expertise, and that’s where EmpireWorks comes in. They specialize in professional EIFS maintenance, repair, and inspection services to keep your system functioning at its best. Their team offers:
- Routine inspections that are tailored to your building’s specific needs.
- Professional repairs for issues like cracking, moisture intrusion, and sealant failures.
- Preventative solutions to reduce future maintenance costs.
EmpireWorks ensures your EIFS system remains in top condition, protecting your building and saving you money in the long run.
Conclusion
Regular inspections are essential for maintaining the performance and longevity of your EIFS system. Most systems benefit from inspections every one to three years, depending on their type and environmental exposure. By addressing minor issues early and scheduling professional inspections with trusted providers, you can preserve your building’s energy efficiency, durability, and aesthetic appeal for decades to come.
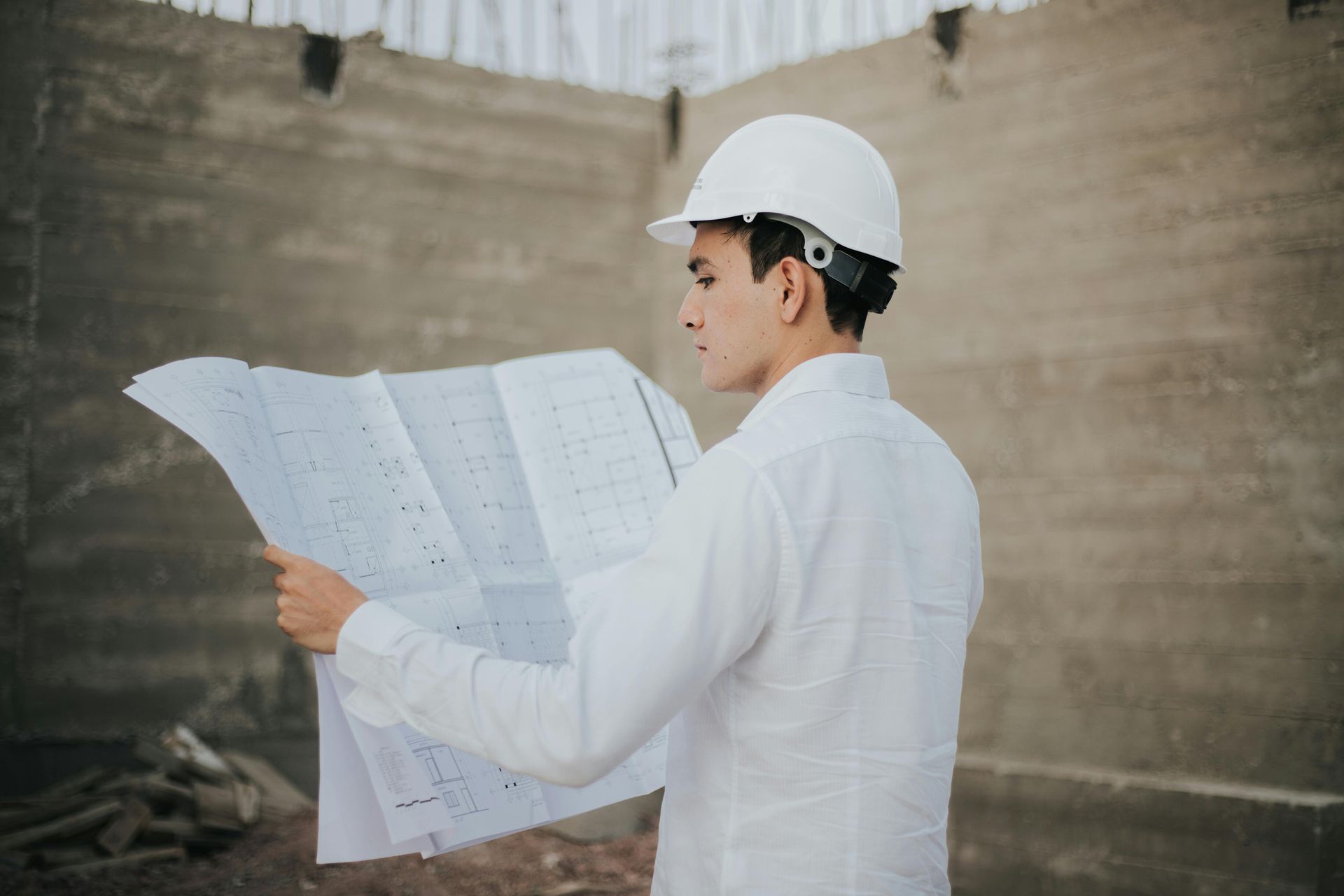
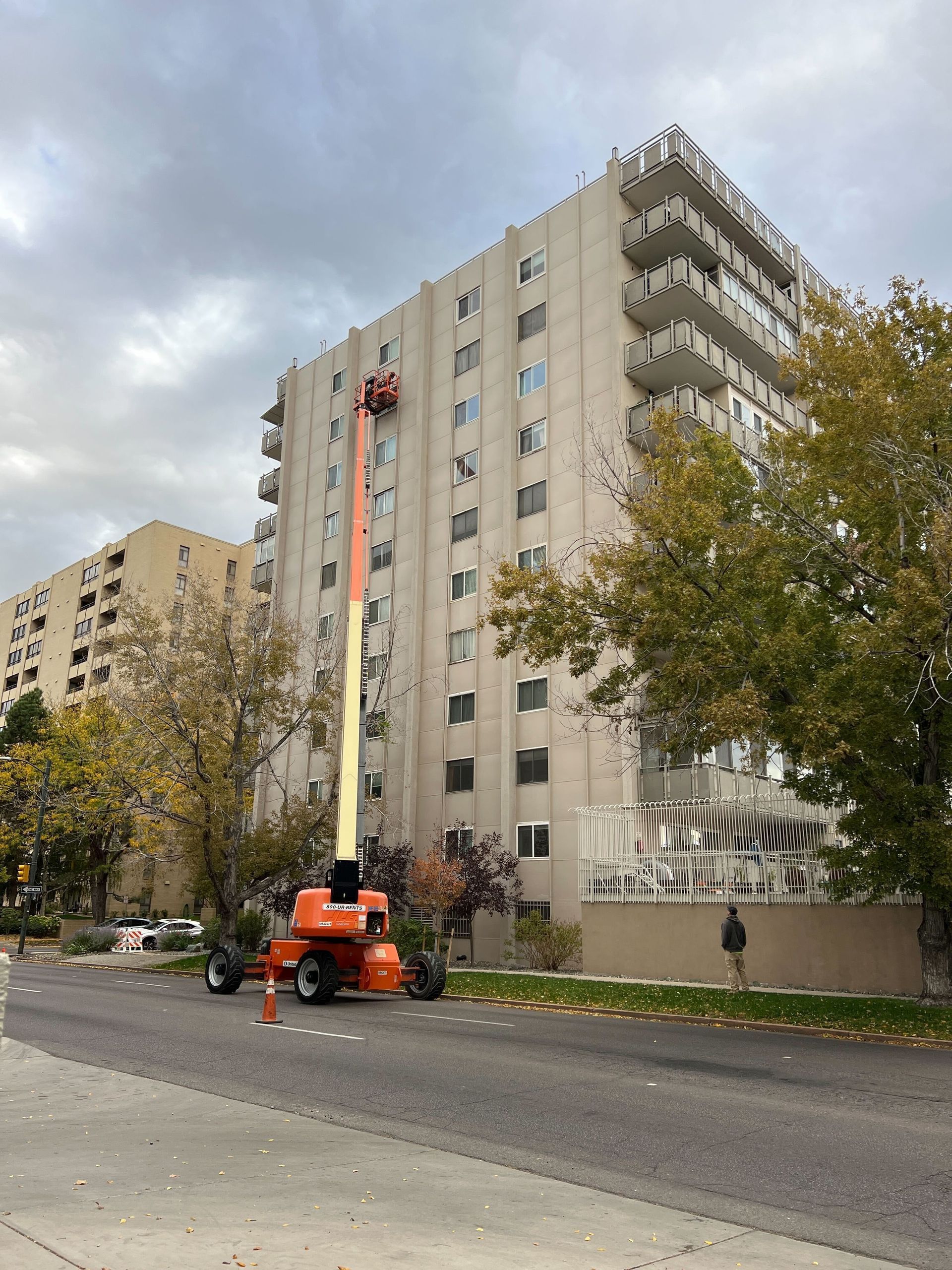
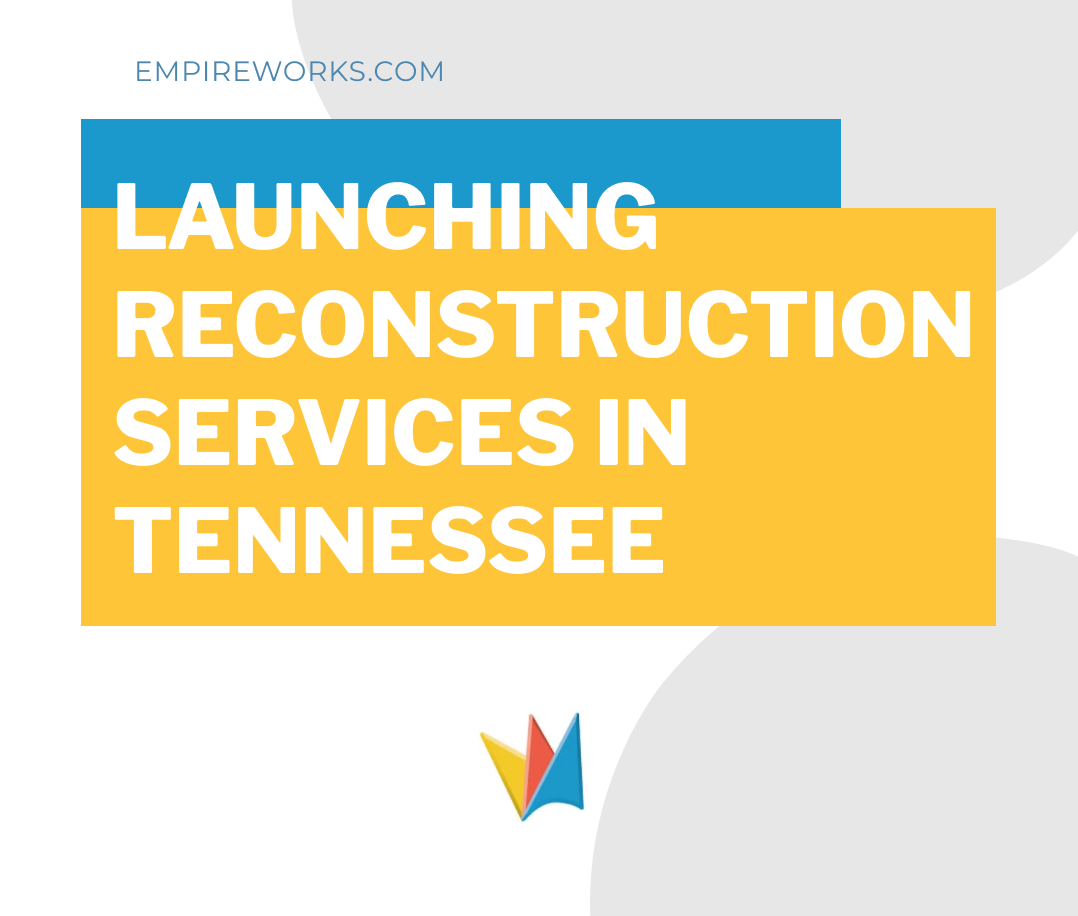
EmpireWorks Reconstruction Launches Top-Tier Reconstruction Services to Middle Tennessee Communities
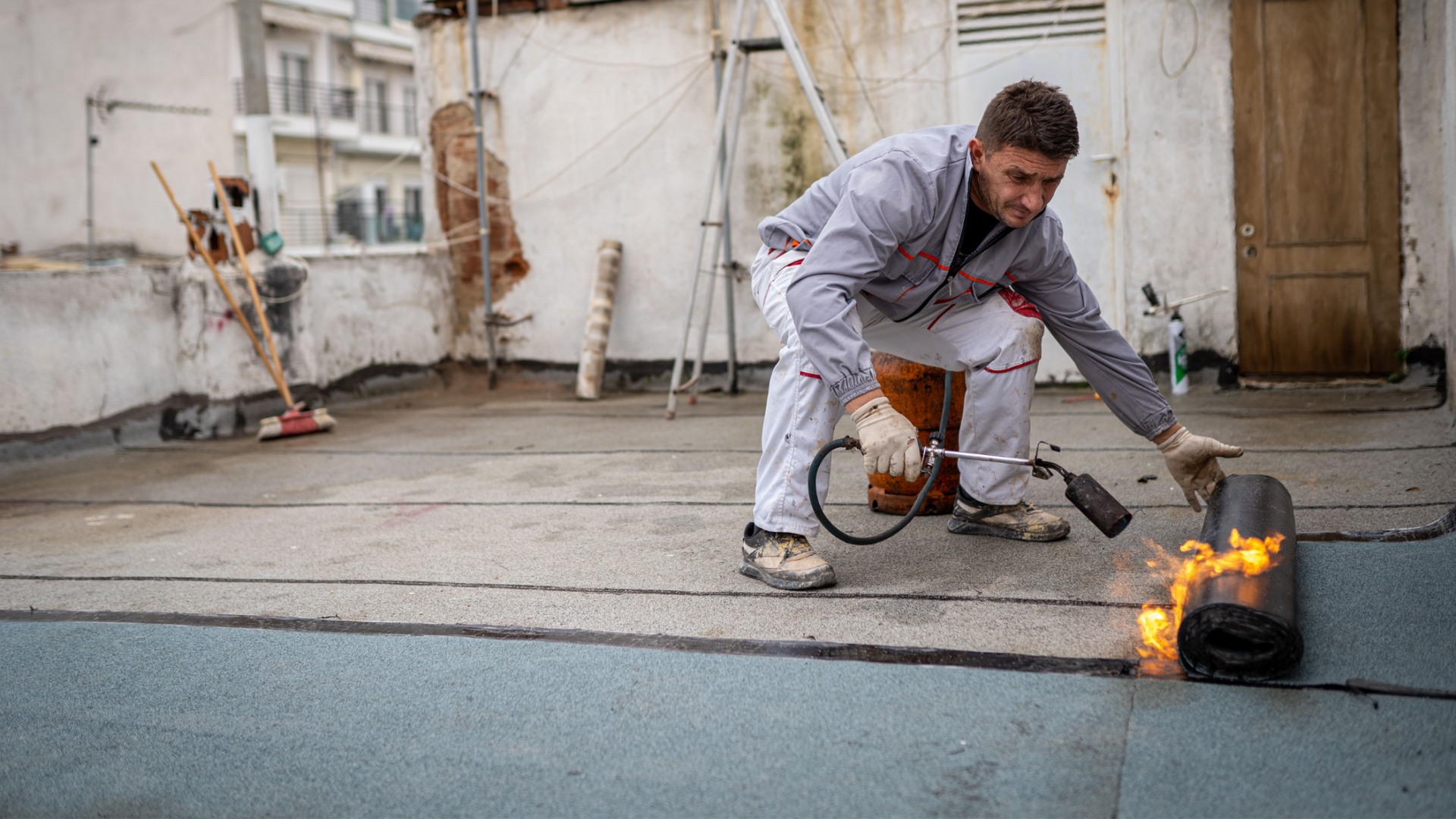
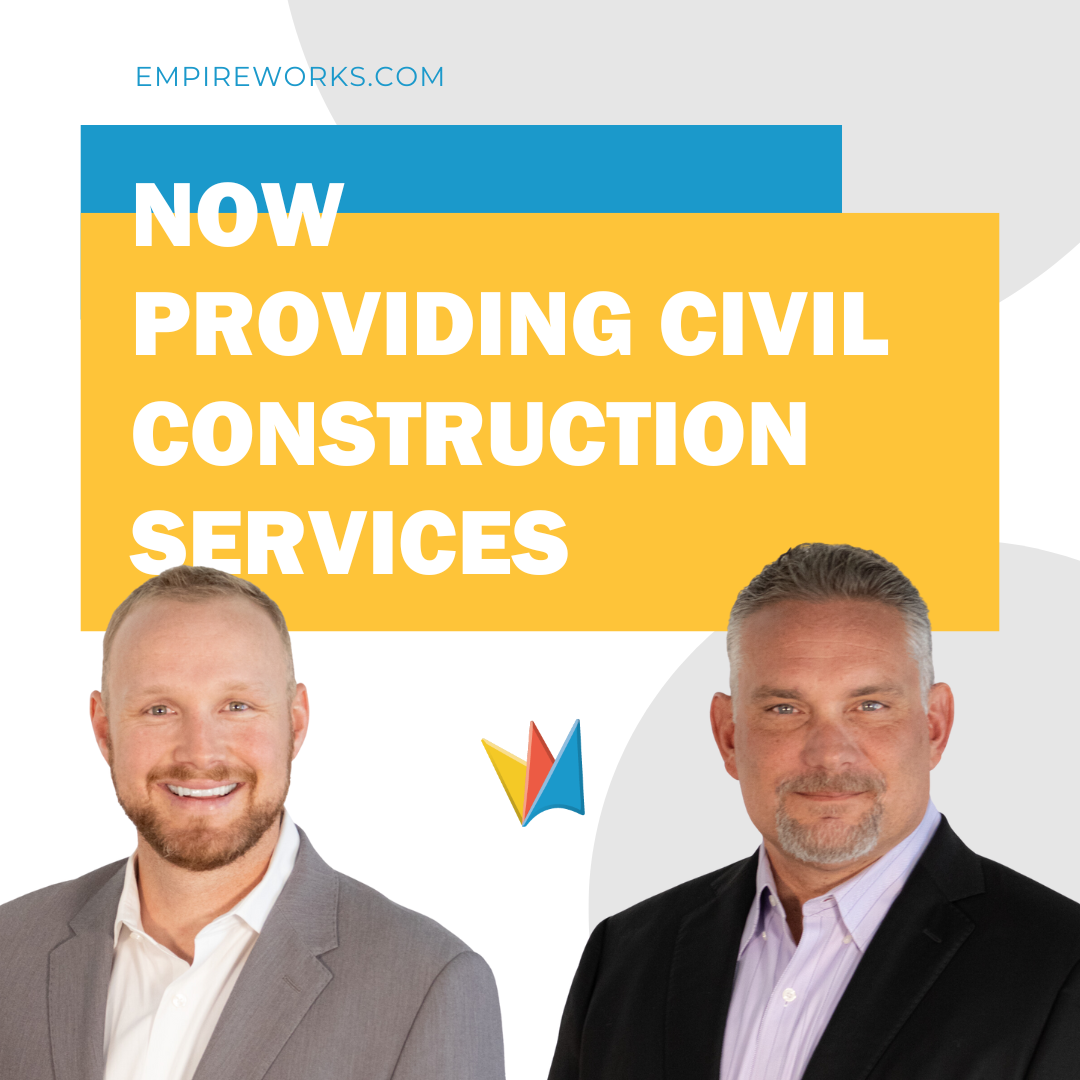